ASIBEX Can Factory Case Study
Coordination of MEP works with other discipline & production of Shop Drawings
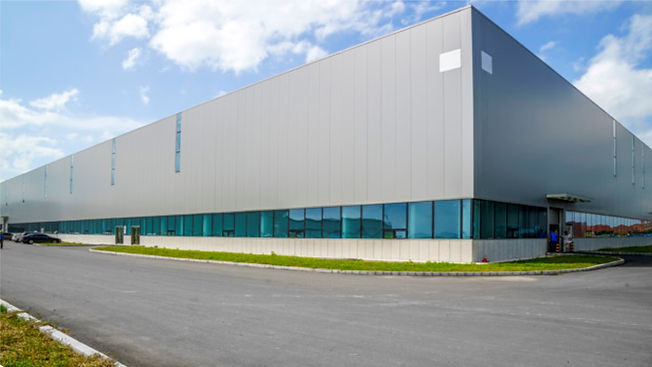
Project Study
The built-up area was around 18,000 SQM metal construction, to house 2 stages of the project. Energy supply units were situated in open space, adjacent to the building. Roof height was 10-15 M.
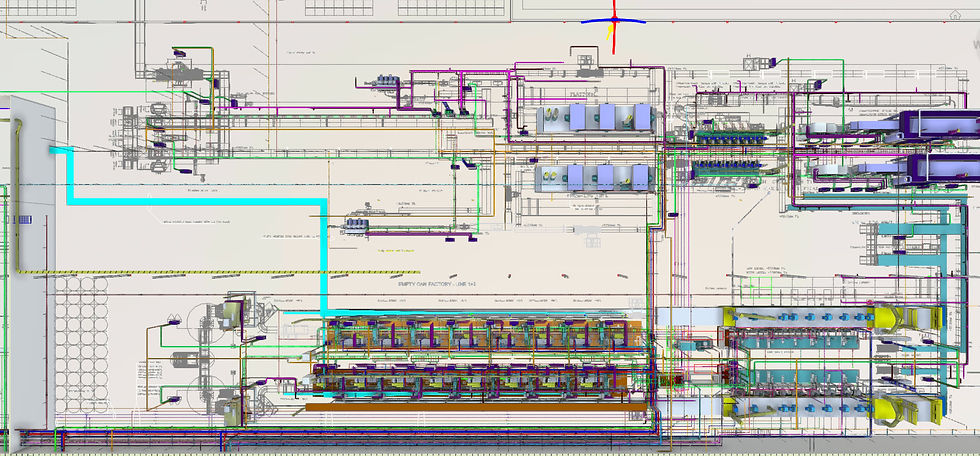

Equipment: Most of the equipment had to be modelled individually to actual size from manufacturer’s data sheets and placed in locations as per the manufacturer’s recommendations and instructions.
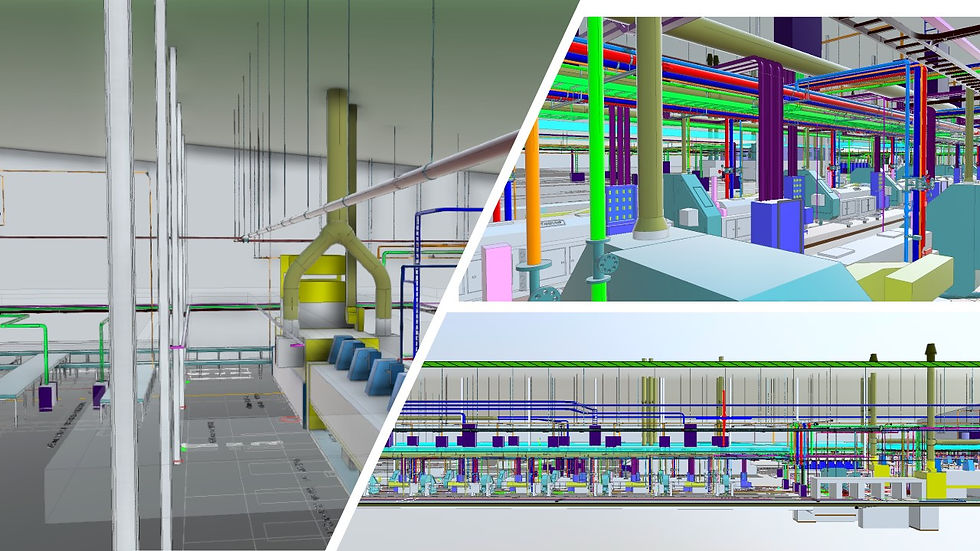

Engineering Networks: Engineering networks were modelled based on recommended equipment locations, load requirements, safety standards and manufacturer's recommendations
Coordination: Model allowed a higher level of coordination and optimization of machinery, equipment, connections etc. which achieved considerable savings, considering the high cost of materials in such projects


Working and Shop Drawings: Model also allowed production of highly accurate shop drawings for all equipment including all MEP services
Installation: Model greatly assisted contractors and equipment suppliers to fine tune all technical issues related to installation

